Electrodeposition
Electrodeposition may be considered one of the most adaptable and cost
effective methods for the large scale deposition of elemental and compound
semiconductors. These films may find application in photovoltaic and
display devices.
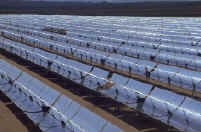
Picture above is a typical solar energy farm
|
Photovoltaics
Introduction:
Photovoltaic
solar cells are composed of various semiconductor materials such as single
crystal, polycrystalline or amorphous Silicon, Cadmium Telluride, Copper Indium
Diselenide (CIS), Copper Indium Gallium Diselenide (CIGS), Gallium Arsenide and Indium Phosphide. More recently organic semiconductors
and dye sensitized solar cells have also received attention. One of the most cost
effective (and in our estimation, one of the most under utilized) methods of producing the semiconductor layers is
electrodeposition.
Electrodeposition - The Background:
The main barrier to photovoltaic cells penetrating the
mass market is the prohibitive cost of the solar panels. More cost
effective method of manufacture are constantly being sought.
Electrodeposition may be considered to be one of the least expensive and
most flexible approaches for the large scale deposition of solar grade
semiconductors. For example, the successful electrodeposition of the II-VI
semiconductor CdTe has been successfully achieved and this approach has
been the basis for the commercial production of thin film CdS/CdTe
photovoltaic cells.
Electrodeposition of II-VI Semiconductors:
There are numerous examples of II-VI semiconductors that
are amenable to electrodeposition. Typical examples include CdTe, CdSe,
CdS, CdHgTe, ZnS, CIS and CIGS etc. Successful electrodeposition may be achieved
using aqueous, non-aqueous and molten salt electrolytes. Perhaps the best
studied is CdTe in which very high purity thin films have been deposited
from acidic solutions of Cd2+ and HTeO2+. The fundamental processes for allowing the CdTe deposition
have been patented by Jerry Barker and co-workers. These processes have
been exploited by BP Solar as the basis of the Apollo thin film CdTe
photovoltaics project in Fairfield, California. This project
successfully deposited substrates up to 1 m2.
The recent success of
First Solar's CdS/CdTe technology
has clearly illustrated the commercial viability of this thin film PV. Other
companies such as PrimeStar Solar
are also attempting to enter the market with CdS/CdTe cells.
Clearly, in our view the electrodeposition of CdTe is a commercial success
waiting to happen.
Electrodeposition of III-V Semiconductors:
Example materials that have been successfully electrodeposited
include GaAs, InP and GaP. PV devices made from these materials often have
high conversion efficiencies, so the motivation to develop low
cost methods of deposition is compelling. To date, in almost all cases, the electrodeposition
process has been carried out in molten salt electrolytes, and careful
control of the bath conditions is required to allow high purity deposits.
In addition, this approach generally increases the material costs due to
the relative complexity of the deposition equipment. Clearly, new
directions are required and further work on non-aqueous systems may well yield improved performance
and costs.
Electrodeposition of Elemental Semiconductors:
Si and Ge have both been successfully electrodeposited
using molten salt and non-aqueous electrolytes. The deposition of these
elements is thermodynamically favored so additional work in this area may
well yield improved results, offering the possibility of low-cost PV grade
materials. Some of the key problems to overcome will be related to
deposit purity, morphology and surface reactivity. Additional work on
bath precursors will also be necessary.
New Directions:
Electrodeposition may be employed for the successful
deposition of a range of semiconductors. By careful selection of
deposition equipment, electrolyte, temperature, precursors, deposition
conditions, doping levels and control of the impurity content, it is
thermodynamically possible to deposit high purity films of Si, CdTe, GaAs,
InP, CIS and many others. We offer the capability to design and construct
plating systems to allow for the large area commercial deposition of these
technologically important materials.
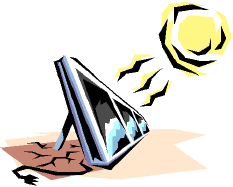
|